What's behind the KEB CNC kernel?
High-end CNC solution for milling, turning and co.
High-end CNC solution for milling, turning and co. CNC machines are just as popular in toolmaking as they are in metal or woodworking. KEB Automation provides the macthing software solution for CNC applications. In addition to entry-level functionalities, high-end solutions are also offered for applications such as milling, drilling, cutting, grinding, bending and associated handling systems. Here, the integrated ISG CNC kernel plays a central role. Its features show why the term “high-end solution” is appropriate.
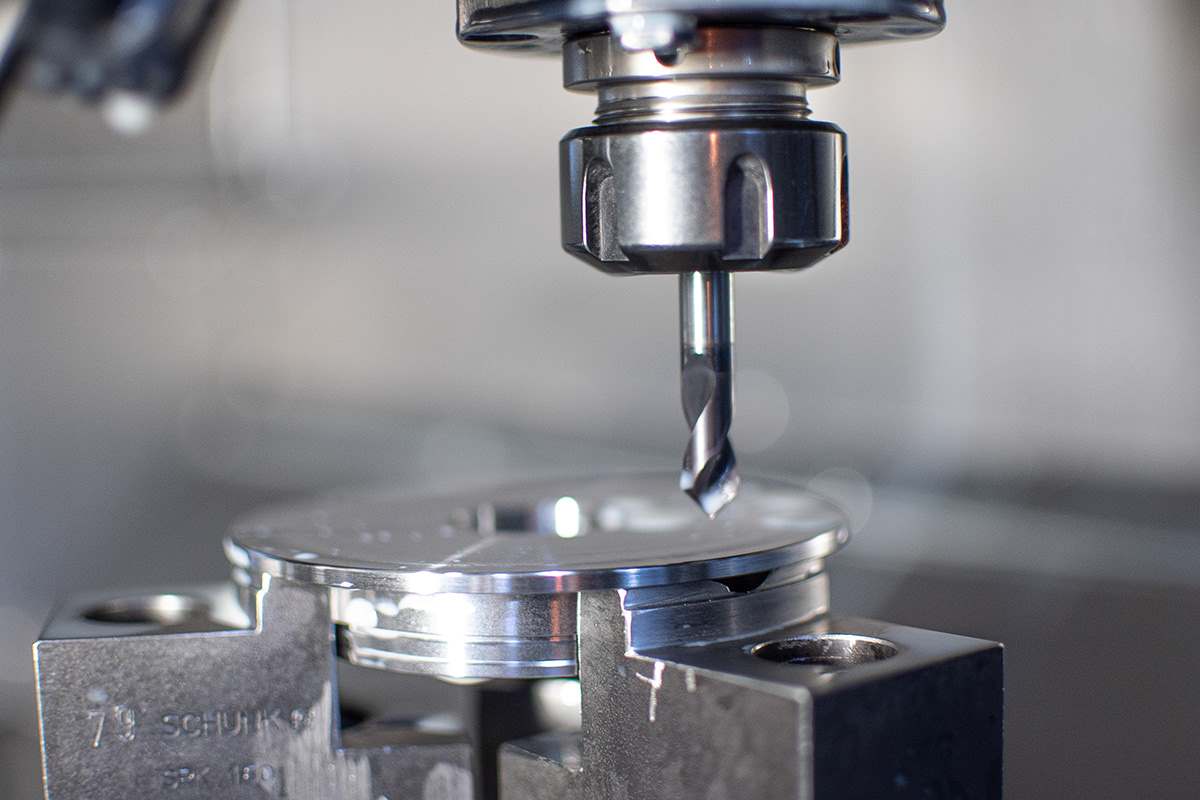
There are many reasons for using CNC machines: In particular, the high precision with which milled parts and other workpieces are manufactured due to the data-based method of operation is a major advantage. However, the high reproducibility and the cost-effective and automated production are also good reasons for using innovative CNC technology. The effort of machine support by the CNC programmer is gradually fading into the background, creating space for taking on other tasks and increasing efficiency in the production process.
“For the implementation of complex applications, we offer a scalable high-end software solution that consists of an integrated ISG CNC kernel for motion control or visualisation, including a user-friendly HMI interface,” says Sebastian Wietzorrek, Application Engineer for Automation and Drives at KEB. The CNC kernel is implemented on real-time IPC controllers. The kernel was developed by KEB in collaboration with ISG. This has resulted in a powerful software solution for controlling machines and plants in the areas of CNC, robotics or motion control, which stands for high performance on the control side.
One kernel, numerous functions
When it comes to setting up the CNC applications, the CNC kernel offers users the option of choosing from over 20 pre-defined kinematics. The CNC kernel was implemented on real-time-capable IPCs that are used with Linux. High-speed cutting (HSC), water jet cutting or milling machines are just a few examples of possible applications for which the CNC solution is designed. Another feature of the kernel is the options for different interpolation types (linear, circular, helical or splines) with the aim of achieving a smooth and jerk-limited motion control. In addition, flexible parameterisation of the control for optimal adaptation to the machine properties is possible. “Part of the CNC kernel is the predictive feedforward control, which is also possible with spline coefficient generation. In addition, a tool geometry correction with contour mapping is offered,” says Wietzorrek. Through compensation for axis and machine errors, coupled with exact path and speed planning, the software solution ensures particularly high precision. Systems with up to 64 axes are possible for the realisation of a CNC application and depending on the requirement, the number of axes or channels can be increased.
Simple implementation with COMBIVIS
The integration of the CNC kernel in the KEB complete solution results in high usability, since the system is set up via the automation tool COMBIVIS studio 6. The object-oriented design of COMBIVIS studio 6 supports users in the configuration of axes and channels. “CNC machine manufacturers can automate their machine technologies with open tools based on standards, without having to dispense with multichannel and compensation, for example,” says Wietzorrek. In addition, PLC and machine functions can be easily extended using the IEC-61131 standard. COMBIVIS is also available for HMI, so that a user interface is created for operation of the CNC machine.
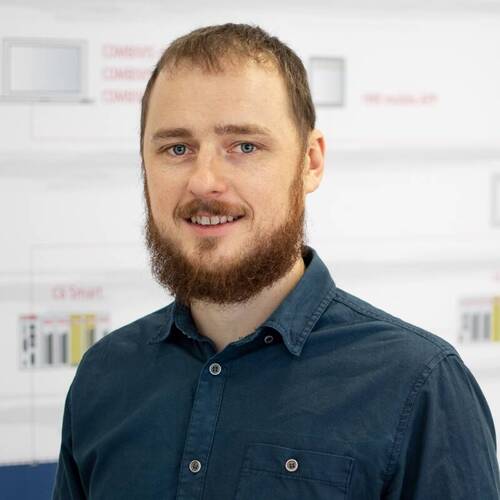
Sebastian Wietzorrek
Application Automation and Drives
+49 7131 79793-116
+49 175 3202487
sebastian.wietzorrek@keb.de