Consistent concept for machine safety
Integrated automation with certified components
Functionally safe system solutions for machines and plants are based on a consistent architecture up to the mechanical interface. This results in potential savings in terms of space, time and money as well as extended application possibilities. Certified hardware and software are used to simplify the project planning and development of applications with safety solutions for the user. This creates transparency for highly integrated machine safety.
- Integrated automation with safety control and safety I/Os
- Drive-based safety functions in drive controllers
- Engineering tool from one source for the creation of system solution
“In the field of functional safety we offer a broad portfolio, including drive controllers with integrated safety functions and an independent safety control system supplemented by modules with safe inputs and outputs”, explains Manuel Keinhorst, engineer for control technology at KEB. Integrated in the EtherCAT based control and remote I/O system the C6 Safety PLC and the C6 Safety I/O modules take over all safety relevant tasks of the control level. The Safety PLC has a two-channel design and can be used as a freely programmable safety controller for applications with requirements according to SIL3 (IEC 61508) and PL e (EN ISO 13849). Communication of the standard application and safety application takes place via the EtherCAT master. “Here, safety-related communication via the Safety over EtherCAT (FSoE) protocol, based on the black channel principle, forms the interface between safe Safety PLC and the FSoE slaves in the system. In particular, this provides a flexible interface to the drive level”, says Keinhorst.
Certified software tools round off the safe hardware components. The automation platform COMBIVIS studio 6 enables programming to be carried out in one development tool. It combines the freely programmable application development according to IEC 61131-3 for the controllers, a safe parameterization interface for the drives and a package for programming the safety application. In addition, prefabricated and certified modules are available according to the specifications of the PLC Open organization. In the EtherCAT topology, the modular safety controller represents a participant that is compatible with different PLC and IPC systems from KEB. The configuration of the safe inputs and outputs takes place with the help of the Safety Editor in the safety application.
“This development environment facilitates the development, verification and acceptance of the security application for the user due to its simple structure and the already certified modules”, explains Manuel Keinhorst. KEB also offers support in the implementation of automation projects for machines and systems in the form of consulting and training.
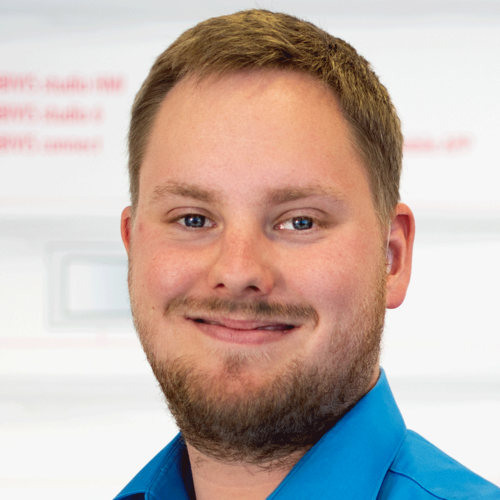