DRIVE CONTROLLER
COMBIVERT F6
Implement new machine concepts with enhanced performance, communication and integrated safety requirements. COMBIVERT F6 drive controllers are a frequency inverter and servo drive combined in one device and cover the entire power range from 2.2 kW to 450 kW. They control a wide range of motor technologies, with or without encoder operation, and – depending on the application – feature scalable, high-performance safety functions.
Highlights
- Functional consistency across the entire power range
- High level of scalability: A wide range of installation types and cooling modes
- Various options for motors, encoders and communication
- Precision and the highest level of repeatability
- Integrated safety technology
- Can be used in a wide range of applications
Technical data
Power class | 3-phase 230 V | 3-phase 400 V | |
---|---|---|---|
Power range | 2.2 kW … 22 kW | 4 kW … 450 kW | |
Rated currents | 11 A … 85 A | 9.5 A … 800 A | |
Peak currents (60 s) | … 1.8 x In | … 1.8 x In |
Device variant | COMPACT | APPLICATION | PRO |
---|---|---|---|
Fieldbus communication | EtherCAT or VARAN | EtherCAT, PROFINET (IRT), EtherNet/IP, POWERLINK, ModBus/TCP | EtherCAT, PROFINET, ModBus/TCP |
Communication interfaces | CAN, diagnosis RS485/232 | CAN, diagnosis RS485/232 | CAN, diagnosis RS485/232, Ethernet, ModBus/RTU |
Functional Safety | STO | STO, SBC and optional encoder-based speed/position-dependent safety functions | STO, SBC and encoderless speed-dependent safety functions |
Safety profile | --- | Safety over EtherCAT (FSoE), PROFIsafe | Safety over EtherCAT (FSoE) |
Encoder interfaces | Multi-encoder | Multi-encoder | Multi-encoder optional |
Communication
Type | |
---|---|
Real-time Ethernet interface | EtherCAT, PROFINET, EtherNet/IP, ModBus TCP, POWERLINK, VARAN |
Communication interface | CAN, Diagnostic interface RS485/232, Ethernet |
Drive profile | CiA 402 (IEC 61800-7) |
Safety profile | Safety over EtherCAT (FSoE), PROFIsafe |
Cyclic fieldbus cycle time | EtherCAT up to 250 µs (125 µs on request) PROFINET, EtherNet/IP, ModBus/TCP, POWERLINK, VARAN up to 400 µs |
Process data size | EtherCAT up to 32 objects / 64 Byte, PROFINET, EtherNet/IP, ModBus/TCP, POWERLINK, VARAN up to 8 objects / 32 Byte |
Fieldbus Ethernet diagnosis | EoE (Ethernet over EtherCAT), PROFINET Ethernet channel, EtherNet/IP Ethernet diagnostic channel, Modbus/TCP Ethernet diagnostic channel |
Serial diagnostic interface | DIN 66019 for connection to diagnostic tools (e.g. COMBIVIS) or an operator |
Operators / Adapters | LCD operator, Ethernet operator, USB operator, Bluetooth adapter |
Tools | COMBIVIS 6, COMBIVIS studio 6, COMBIVIS mobile, COMBIVIS Command Line Interface |
Functional Safety
What is the objective of functional safety? The short answer is to minimise the risks posed by technical equipment to people and the environment. Functionally safe system solutions for machines and plants are based on consistent architecture right through to the mechanical interface. Certified hardware and software isare used to simplify project planning and the development of applications with safety solutions.
COMBIVERT F6 drives offer scalable safety functions directly in the drive controller – with or without encoders. Safety functions and limit values can be flexibly adjusted via digital I/Os and/or the “Safety over EtherCAT” (FSoE) or PROFIsafe safety profile.
- Available for the entire COMBIVERT F6 power range
- Safety functions that can be used with or without encoders
- Up to eight safety configurations per function
- For operating various motor technologies such as ASM, PM, IPM, SyncRel
- Safety functions certified to SIL 3 in accordance with IEC 61508, or to PL e in accordance with ISO 13849
- “Safety over EtherCAT (FSoE)” or PROFIsafe safety profile
- Fast release times
Device variants
Softwarefeatures
Basics | Flexibility | Highlights |
---|---|---|
Sub-mounted braking resistor protection | ||
U/f functionalities | Operation of asynchronous, synchronous (SMM/IPM), synchronous reluctance motors, high-speed motors, high-torque motors, linear motors | Blockade detection |
Brake handling | Evaluation of different types of encoders: TTL, HTL, Resolver, SinCos, EnDat, Hiperface, BiSS | Cooling liquid management |
Quick stop/error reaction | Modes of operation: Velocity, Profile Position, Cyclic Sync Velocity, Cyclic Sync Position, Cyclic Sync Torque, Homing, Jog Mode | Non-linear torque feed forward |
Device memory/ Recipe management | Anti-cogging | |
PID controller | AiSCL (Asynchronous single current closed loop) | |
Motor/rotor identification | Power-off function (for all motor types) | |
Index positioning | Servo pump control | |
Position standstill controller | High output frequencies (variant if applicable) | |
Rotary table function | CAN-cross-communication (device variant APPLICATION and PRO) | |
Touch probe function | ||
Drive software update | ||
and much more. |
High-speed drives
Processing spindles, turbo blowers or vacuum pumps: COMBIVERT F6 High-Speed Drives offer the ideal solution for these and many other applications in which output frequencies of up to 2,000 Hz are required. In combination with the appropriate sine filters, motors are particularly well protected at high speeds and system efficiency is effectively increased. Innovative simulation methods are available for fast and resource-saving commissioning of the high-speed drives.
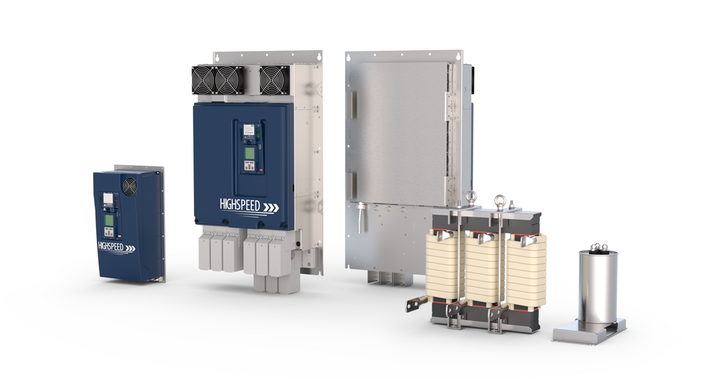
Highlights
- Drive controller with outputs of up to 450 kW / 800 A
- Integrated safe speed monitoring
- Motor protection and optimum system performance with sine filter
- Precise encoderless control of a wide range of motor types
- Up to 120,000 rpm and output frequencies up to 2,000 Hz
- Integrated supply for magnetic bearing controls
- 3C3 protective coating for aggressive environments
Technology
Energy recovery
Rather than burning energy, why not harness it? With energy supply and recovery systems from our product range, machine and plant manufacturers are already optimising new machines during the design phase or creating a second phase of use for existing systems in retrofit manufacturing.
DC INTERCONNECTION
Save energy while reducing the installation workload at the same time. DC interconnection makes sure of this and more, while paving the way for exchanging energy with other frequency inverters. Only one AC power supply is required for the DC coupling. KEB’s drives are freely scalable and designed for universal use. This gives the user maximum efficiency and flexibility in the actual application. An added advantage is that eliminating braking resistors reduces heat build-up and ensures less space is needed in the control cabinet.
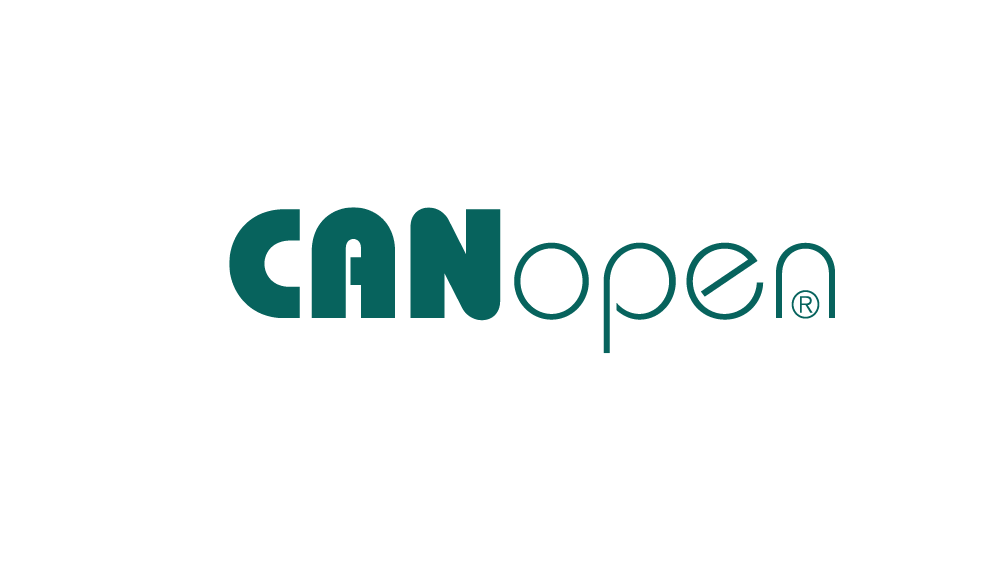
profile Position Mode CIA 402
The drive profile according to CiA402 provides a standardised platform for drive controller-based automation. This is achieved by means of the modes of operation specified in the profile, in particular also by the Profile Position Mode. The resulting relief of the PLC and cost optimisation with direct, undelayed access to the application enable economical and high-quality application solutions – consistent and manufacturer-independent.
SENSORLESS CONTROL (SCL/ASCL/ASiCL)
Sensorless closed-loop operation and maximum dynamics – without lowering speed during load fluctuations. This is made possible by KEB’s sensorless control methods ASCL (Asynchronous Sensorless Closed Loop) and SCL (Sensorless Closed Loop), regardless of whether asynchronous, synchronous, synchronous reluctance or IPM motors are involved. With ASiCL (Asynchronous single current closed loop), KEB also provides a complementary solution which ensures excellent shaft performance with high torque even in the low-speed range. The motor model also takes care of positioning during subordinate positioning tasks.
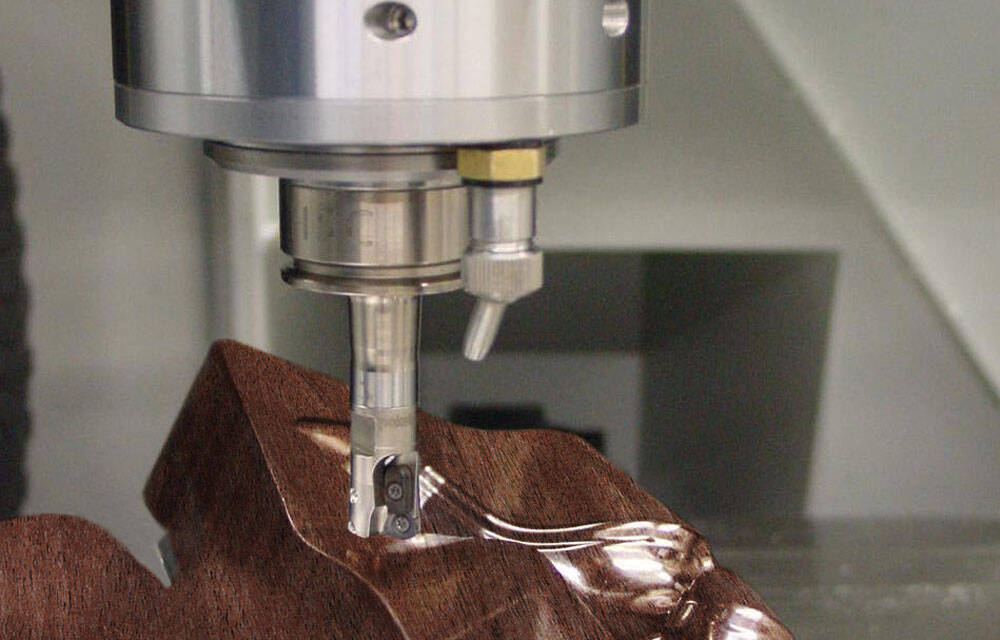
High-speed applications
Whether for asynchronous, synchronous, synchronous reluctance or IPM motors: All types of motors can be controlled and operated highly dynamically without encoders by the COMBIVERT F6 or COMBIVERT S6 drive controllers at high speeds of up to 120,000 rpm using the ASCL or SCL method. Depending on individual requirements, this is possible with or without encoder. This means that nothing stands in the way of using motors in high-speed applications.
In use in these areas of application
MATERIAL HANDLING
Whether warehouse logistics or cranes, speed and flexibility are essential in material handling. KEB ensures a smooth flow of goods and materials in this area.
PLASTICS MACHINERY
For extrusion and injection moulding technologies, we offer hardware and software solutions out of one hand that ensure a high level of availability and torque accuracy.
PACKAGING & FOOD PROCESSING
KEB provides the food processing and packaging industry with robust components that are suitable for use in harsh environments.
WOODWORKING MACHINERY
From the control system with numerous software features, to the processing of any machine process data and the drive converter, to the motor with gearbox and brake, KEB is the high-performance partner in woodworking.
TURBO COMPRESSORS AND BLOWERS
High-end products for high-speed applications: Our drive solutions for turbo blowers and radial compressors deliver reliability and utmost precision.