This solution makes motor testing 75 percent faster
IIoT platform NOA optimizes assembly at Brusatori
Brusatori, an Italian electric motor manufacturer, has recently started using NOA, the open automation platform from KEB Automation, at its Milan plant. The IIoT solution is designed to optimize quality control and assembly processes, and to reduce testing times. It has already become clear that the implementation of NOA has been a major success. In addition to efficiency gains, the company has also been able to achieve cost savings in production.
"Previously, the quality of the motors was only checked by operators. This means that if, for example, there was a malfunction or mismatch between customer request and manufactured product, this was only noticed later – an unnecessary waste of time and money,” is how Marco Sala, Managing Director of Brusatori Motors, describes the challenge in their own production. Since 2022, Brusatori has been part of the KEB Group and, in particular, supplies asynchronous, servo and torque motors that are an integral part of the KEB portfolio.
The final quality inspection is extensive. Until now, measured values and limit values were checked manually. This was precisely where room for optimization existed, and the goals were quickly defined: quality inspection should be carried out at each individual station of the assembly process in order to have fewer defective motors to sort out at the end. In addition, the test time should be shortened by automating the previous manual comparison of measured values.
Open automation platform as a solution
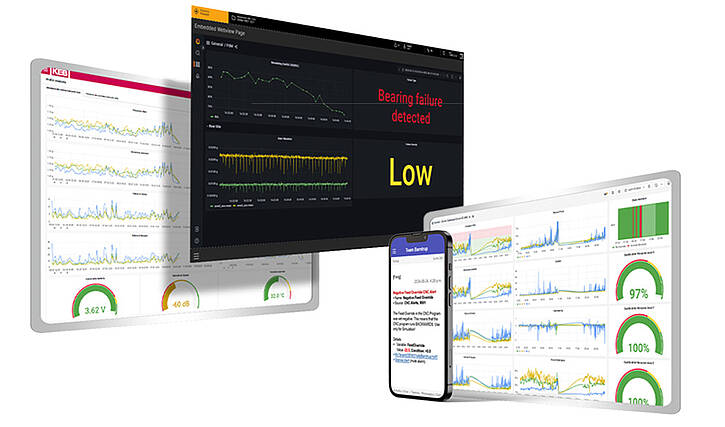
The solution for achieving these goals is provided by the open automation and IIoT platform NOA from KEB. NOA stands for Next Open Automation and enables machine and plant manufacturers to design individual automation solutions based on open systems. With NOA, KEB offers a basic toolkit that can be expanded to include customer-specific and third-party apps. But how exactly was NOA used at Brusatori?
At the end of the assembly line, a structure was used that consisted of an NOA Edge Device – the C6 COMPACT 3 from KEB – which in turn was connected to four measuring devices. Various apps for this application are installed on the Edge Device. Brusatori wrote its own apps for the data connection between the measuring devices and NOA and added them to the customer-specific app catalogue. A database app that contains the threshold values of the measured values for the motor variants and retrieves a comparison logic was also added to NOA by the customer and replaces the manual comparison of the measured values with the printed data sheet that was previously carried out. A CSV export app is installed on the device to output a history of the measurements. And HELIO provides an application that Brusatori can use to create HMIs in no time at all. This makes it possible to start measurements, visualize results, and quickly determine whether a motor is OK and can be transferred to the next production step.
Automated quality inspection
“Thanks to the implementation of NOA, Brusatori now has an automated system for motor testing and quality inspection. This has reduced the complete testing time from 20 minutes to five minutes,” says Data Scientist Mehdi Rahmanian from KEB Italia, who implemented NOA at Brusatori. ”We have eliminated the bottleneck at the end of the quality inspection and defective motors will in future be detected and sorted out during the process.”
And Sala is also satisfied: “Implementing NOA took just two weeks and proved to be a particularly easy and cost-effective solution. In addition, the automation platform offers us the advantage of being able to incorporate our own logic.” Specifically, Brusatori Motors was able to integrate apps to connect the measuring devices, reducing the overall Automation components. This is where the strength of NOA as an open platform comes into its own.
How the motor test is carried out now
The new automated quality control of the motors now follows a more efficient process in many ways. When a motor arrives at a station, the technician performs the respective work step. The employee scans the engine using a QR code to identify the exact customer variant – an important step for entering the threshold values in the database app. The quality inspection then begins and the measuring instruments are connected to the motor. The measurement itself is conveniently started with a click in the HELIO HMI. The measured values are then output by the measuring instruments and the database app checks the values against the threshold values and then indicates in HELIO whether the motor is OK. If all values are within the acceptable range, the motor passes through the further production steps.
“NOA Core runs entirely on-premises, i.e. without the NOA portal or a cloud connection. We are pleased that we were able to simplify the testing of motors at Brusatori and take the assembly process to a new level overall with our open automation platform,” sums up Daniel Preuß, Product Owner IIoT Platform at KEB.
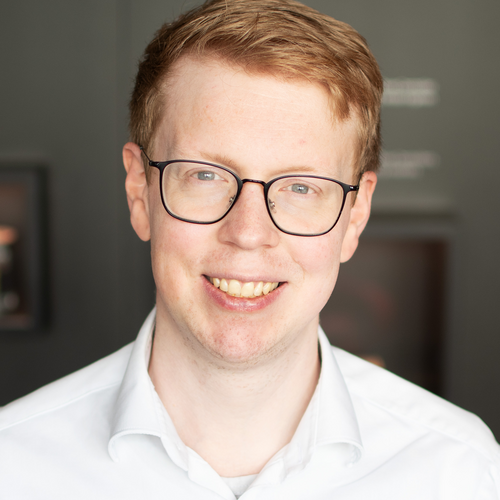