Protected against dust, heat and moisture
Motors, inverters and brakes from KEB under harsh conditions
Shredding plants, sewage treatment plants and other applications are often subject to particularly harsh environmental conditions – metal chippings or chemicals are just two of the challenges. This places increased demands on the components installed in the drive train. Drive controllers, motors or brakes: they all require a high level of protection against influences such as moisture, dirt and sometimes extreme temperatures. With a few precautions, KEB ensures that the drive components remain intact for a long time even under these conditions.
A drive train is only as strong as its weakest link – with this in mind, KEB provides an increased level of protection for many products that operate under challenging environmental conditions. Depending on the application, it can be chemical substances, chips in the air or penetrating moisture that put a strain on the drive components of a machine or system. Without appropriate measures, there is a risk of malfunctions, a shortened service life of the system and in the end high costs for the user. So what does KEB do to protect inverters, motors and brakes?
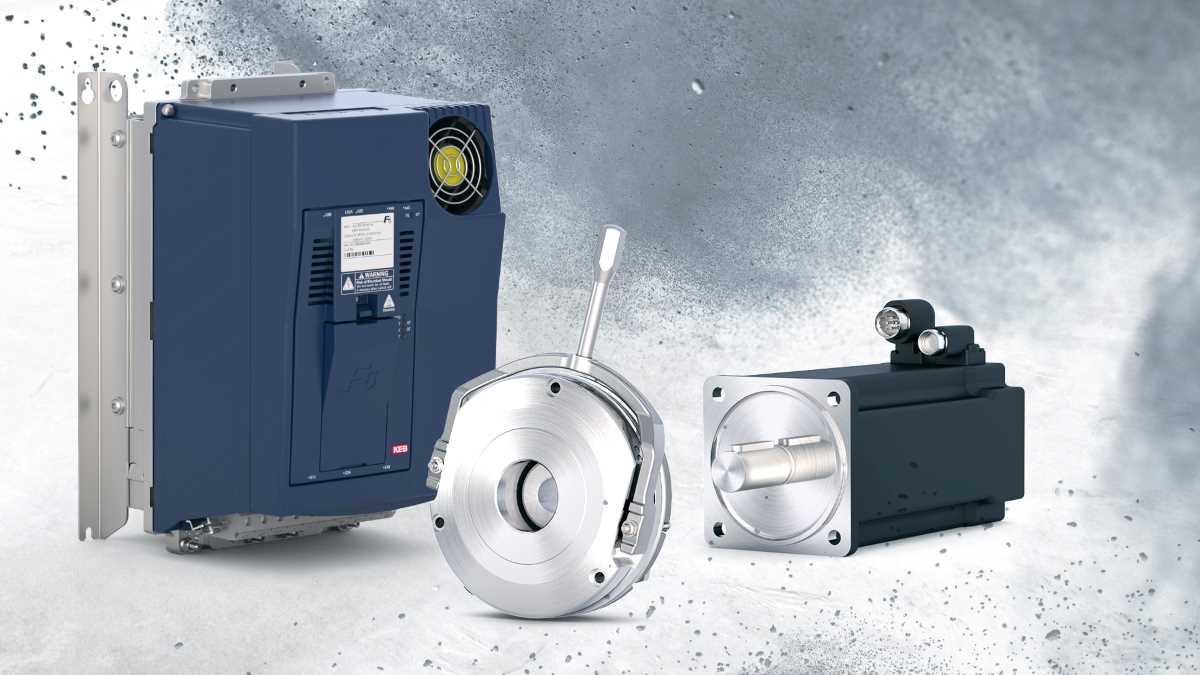
Drive controller: circuit board protection and simulated climate extremes
Even a well-sealed industrial control cabinet does not offer one hundred per cent protection against external influences. And the heat generated in the control cabinet itself can also be a challenge for the drive components that should not be underestimated. This is why the drives from KEB are designed for different ambient temperatures. The integrated safety functions, which have individual requirements with regard to the respective ambient temperature, are also taken into account.
One application in which effective protection is important is shredder systems. ‘Electrically conductive dust can be generated during shredding, which could damage an inverter if no precautions are taken. That's why the circuit boards of our COMBIVERT Drives are coated as standard and therefore offer a particularly high level of protection,’ says Benjamin Mönnig, Head of Application Sales at KEB.
Further protective measures are available for use in other applications where harsh environmental conditions prevail. ‘If required, we offer a 3C3 protective coating for the PCBs and connection points in accordance with IEC/EN 60721-3-3, which provides additional robustness. Tailored to the environmental requirements, users benefit from a longer service life of the drives thanks to the coating,’ says Mönnig.
Load tests are already carried out during the development phase in order to check whether the components can also reliably withstand extreme conditions before the drives are actually used. For example, KEB uses climatic chambers to simulate ambient temperatures or humidity. The drives can also be tested in a salt chamber to show that they are sufficiently robust.
Special coating: as robust as a stainless steel motor
Servo and geared motors are optionally available from KEB with a STEEL-IT coating. This is a special epoxy coating that protects against damage caused by corrosion in particular and represents real added value, especially when working in harsh environmental conditions. The highlight: thanks to the coating, the surfaces of the motors are as robust as a stainless steel motor, but cost significantly less. Due to its resistance to salts, chemicals and high-pressure cleaners, coating is an interesting solution for the food industry, among others. Here, strict hygiene requirements demand close-meshed cleaning and the use of cleaning substances. As these often have corrosive effects and can attack the installed components, epoxy coating is an effective way of significantly extending the service life of the motor. In addition to the STEEL-IT coating, the ‘P6’ corrosion protection is also available for motors manufactured by KEB Antriebstechnik in Schneeberg, which includes further measures in addition to the coating itself.
Brakes with various protection options
In most cases, KEB's wide-ranging brake portfolio also includes options that protect the brake against a variety of external influences. ‘Our COMBISTOP 38 spring-applied brake, for example, can be fitted with a protective ring to increase the degree of protection for dusty and moist environments or to ensure contact protection,’ says Kevin Zysk, Head of Sales Brakes and Clutches at KEB. ‘With the COMBISTOP 28 series, we achieve up to protection class IP66 as standard and up to IP67 as a customised version.’ Insulation class H can be achieved, which means that the individual components are approved for temperatures of up to 180 degrees Celsius.
For particularly harsh and cold environments, the COMBISTOP brakes can be produced as a CCV version (Cold Climate Version). This means that temperatures down to minus 40 degrees Celsius are not a limitation. If the continuous shaft on the brake also needs to be sealed against the external environment, it can be fitted with a shaft seal. If no shaft emerges, a completely closed housing can also be realised.
The COMBIPERM permanent-magnet brakes and working-current-operated COMBINORM brakes also have a number of robust features. For example, they can be designed for an ambient temperature of minus 40 degrees Celsius or up to 120 degrees Celsius. The optional felt ring protects the braking torque and the friction surfaces against leaking oil from neighbouring bearings. ‘As an option, our brakes can also be made of stainless steel, with a special alloy or as an encapsulated version, making them even more resistant in harsh environments,’ says Zysk.
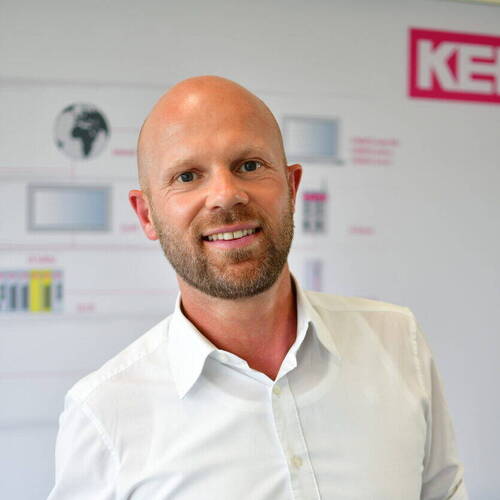