Hinter den Kulissen des Bereichs Bremsen & Kupplungen
Bei KEB Automation gilt: Individuelle (System)Lösungen sind der Standard. Aber wie genau zeigt sich das bei den Bremsen und Kupplungen? Der Geschäftsbereich legte nicht nur vor über 50 Jahren den Grundstein des Unternehmens, sondern ist seit jeher auch einer der Bereiche mit einer besonders hohen Fertigungstiefe, um auf die verschiedenen Kundenbedürfnisse flexibel eingehen zu können. In der Praxis bedeutet das: Entwicklung, Fertigung, Vertrieb und vieles mehr erfolgen in-house. Über den Weg der KEB Bremsen und Kupplungen zu serienreifen, individuellen Produkten.
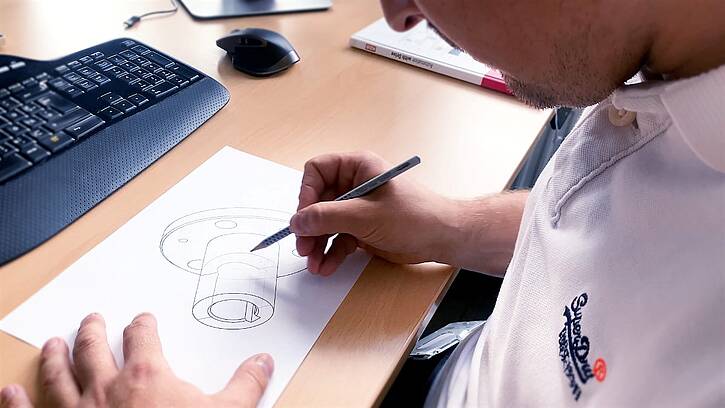
Federkraftbremsen, Permanentmagnetbremsen und -kupplungen oder arbeitsstrombetätigte Kupplungen und Bremsen: Sie alle sind in kundenspezifischen Ausführungen erhältlich. Möglich macht es die Tatsache, dass Bremsen und Kupplungen bei KEB zu über 90 Prozent innerhalb des eigenen Betriebs gefertigt werden können. So können die Anforderungen, die sich von Applikation zu Applikation unterscheiden, bestmöglich berücksichtigt werden. In der Vergangenheit sind auf diesem Wege etwa im Bereich der Federkraftbremsen Doppel- oder bistabile Bremsen (FlipFlop) entstanden. Auch erhöhte Schutzarten, besondere Spulenspannungen und feststellbare Handlüftungen zählen hier zu den bereits verfügbaren Lösungen.
Schritt 1: Kundengespräch
„Benötigt ein Kunde eine Sonderlösung, geht es entweder um das Vorhaben, eine bestehende Bremsen- oder Kupplungslösung zu verändern oder ein neues Produkt zu entwickeln. Dazu wird ein Lastenheft zu der jeweiligen Applikation eingereicht, aus dem Angaben zum Bauraum oder spezifische technische Vorgaben für die Entwicklung hervorgehen“, sagt Anja Groyecki, Vertriebsingenieurin bei KEB. Gemeinsam mit dem Kunden wird so von vornherein erörtert, auf welche technischen Erfordernisse es ankommt und welche Information vonseiten des Kunden notwendig sind, um den Entwurf eines ersten Prototyps angehen zu können. Dabei sind kundenspezifische Lösungen in nahezu allen Produktbereichen möglich.
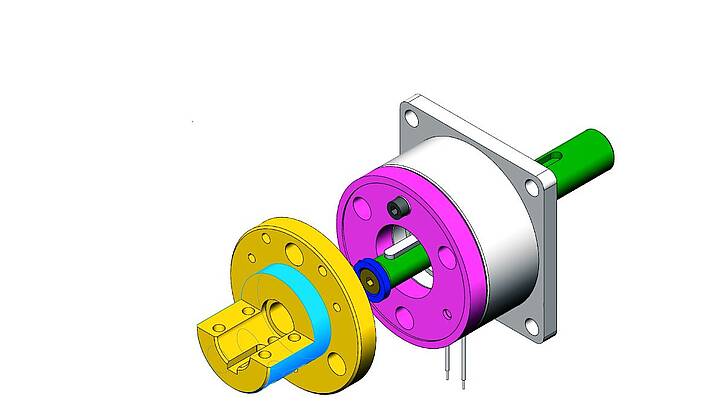
Schritt 2: Konstruktion und Entwicklung
Wurden die Kundenanforderungen aufgenommen und theoretisch betrachtet, kommt im nächsten Schritt die hauseigene Konstruktions- und Entwicklungsabteilung ins Spiel. Unter anderem Entwickler und technische Produktdesigner setzen einen Einbauvorschlag, Einzelteilzeichnungen und abschließend eine Gesamtzeichnung des gewünschten Produktes um. Je nachdem, ob eine komplett neue Bremse oder Kupplung entwickelt oder eine Variante einer bereits existierenden Bremse oder Kupplung erstellt werden soll, unterscheidet sich die Dauer, die dieser Prozess in Anspruch nimmt. Sind Varianten-Designs mitunter in einigen Tagen erstellt, kann sich die Entwicklungsdauer gänzlich neuer Bremsen über mehrere Jahre erstrecken. Die Berücksichtigung des Verschleißes oder die Auslegung von Magnetkreis und Drehmoment sind einige von vielen Aspekte, die zu beachten sind. Zuletzt sind beispielsweise Permanentmagnetbremse COMBIPERM P2 oder die Haltebremse COMBISTOP S1 auf den Markt gekommen. Den Produkt-Einführungen gingen mehrjährige Entwicklungsprozesse voran.
Schritt 3: Musterbau
Das Ziel von KEB ist, hochwertige Sonderausführungen umzusetzen, damit jede Anwendung mit der passgenauen Bremse oder Kupplung ausgestattet werden kann und Kunden von spürbaren Kosteneinsparungen im Gesamtsystem profitieren. Wichtig dabei: der Musterbau und die damit zusammenhängenden Fertigungsprozesse. „Grundsätzlich gehen wir immer davon aus, dass alles für den Kunden umsetzbar ist, was auf unseren Maschinen hergestellt werden kann“, sagt Groyecki. Die Fertigung eines Prototyps und die zuvor anstehenden Prozesse sind zeitintensiv, da hier zahlreiche Abteilungen mitwirken. Unter anderem sind Konstruktion, Einkauf, Arbeitsvorbereitung, Fertigungssteuerung, Versuchsabteilung und Applikationsvertrieb involviert, um Entwürfe zu erstellen, Einzelteile zu zeichnen, Angebote für zu verbauende Komponenten einzuholen, Validierungspläne oder Testbenachrichtigungen aufzusetzen.
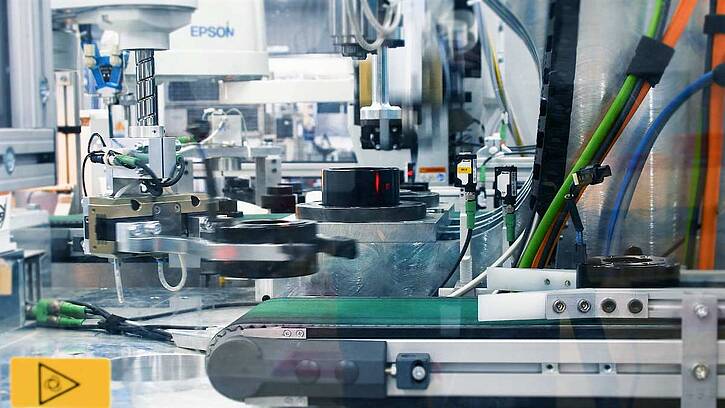
Schritt 4: Tests
Bremsen-Sonderlösungen werden unter anderem von Antriebstechnikherstellern oder auch von Kunden aus spezifischen Applikationsbereichen wie etwa der Medizintechnik bestellt. Damit der gewünschte Prototyp auch zur vollsten Zufriedenheit und mit größtmöglicher Sicherheit funktioniert, durchläuft der Prototyp verschiedene interne Mess- und Testverfahren. Dabei werden unter anderem Drehmomente unter verschiedenen Bedingungen oder Schaltzeiten getestet und auch Dichtigkeitsprüfungen werden durchgeführt. Nachdem alle notwendigen Tests abgeschlossen sind, erhält der Kunde den Prototypen zur Bemusterung. Sind alle Anforderungen an die Bremse erfüllt, wird schließlich der Prototyp durch einen neuen Status abgelöst: die Serie.
Schritt 5: Serienanlauf
„Für uns und den Kunden ist es immer ein besonderer Moment, wenn eine individuelle Lösung in Serie geht. Aufgrund der hohen Fertigungstiefe haben wir auch in der Serie in jedem Schritt des Fertigungsprozesse Zugriffsmöglichkeiten und können Änderungen bzw. Anpassungen unkompliziert und schnell durchführen. Auf diese Weise stellen wir sicher, dass das Ergebnis den Wünschen und technischen Anforderungen des Kunden auf Dauer entspricht“, sagt Groyecki. Ist aus einer Idee ein Prototyp und letzten Endes ein serienreifes Produkt entstanden, markiert die Freigabe für den Vertrieb der neuen Bremse oder Kupplung den vorläufigen Abschluss des Entstehungsprozesses.
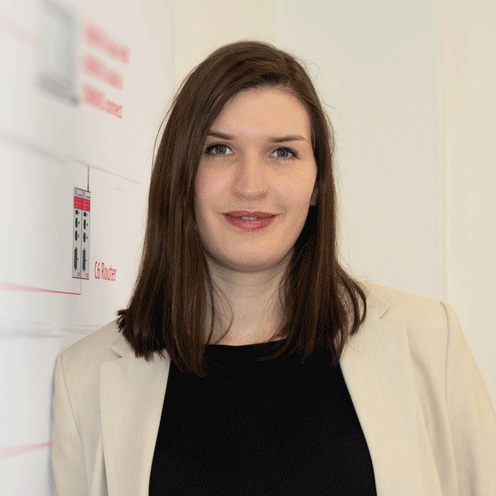