This rack lights up the production at KEB
Assistance system for C-parts management
In KEB Automation's production, many processes have to interact efficiently. To optimise material logistics for assembly, KEB has developed the iCParts assistance system. The system shows employees at the central C-parts warehouse at which shelf location the required screws, washers or nuts are stored. Flat LED line lights form the foundation of this so-called "pick-to-light solution".
With the large quantity of C-parts, it is a challenge for production staff to keep track of them and find the right parts for the next assembly step. In order to avoid tedious searching and to further optimise the production process, KEB has established an innovative system for supplying materials to assembly workstations for frequency inverters. The pick-to-light principle relies on WLS15 luminaires from Banner Engineering, Turck's optical sensor partner.
MORE INFORMATION
Luminaires display sought-after articles
The assembly workstations are equipped with tools and production aids. Required C-parts are ergonomically arranged in small visual storage bins within the employee's reach. Standard labels and QR codes with information about material number, storage location and storage place are attached to the front of each bin. When a storage box is empty, the fitter fills it up again at the central C-parts shelf, where more than 60 items are stored in their own bins. Previously, a paper list had to be used to determine which small parts were in which place on the shelf. By using the iCParts assistance system, every employee should now be able to find the desired item immediately without a long search.
If an employee needs supplies, he goes to the central C-parts shelf with his empty open fronted storage bin, where he scans the QR code of the bin. The assistance system now detects which material is requested and controls the corresponding area of the WLS15 line lights. In this way, iCParts guides each employee directly to the desired item. Without wasting time, he can now refill his empty container.
Controls from KEB in use
The automated reordering of removed C-parts is handled by an RFID-supported Kanban system installed in the C-parts shelf. Kanban is a method of process control that is based on the actual consumption of C-parts. Re-ordering is triggered by radio in real time.
The in-house KEB control and software has already proven itself in other solutions from Turck, so that its use in the iCParts is also obvious. The standard environment developed in-house runs on a Windows tablet attached to the shelf. All the required accesses already exist in this environment, which is why it is possible to build on what is already available. "After programming the necessary drivers, the line lights can be controlled. The connection to the tablet is ensured by a Banner RS485/USB converter on the shelf levels," explains Viktor Derksen, Head of Equipment Construction at KEB. The LED luminaires are each coupled via T-distributors and connection lines. This allows the supply voltage and communication to be looped through from luminaire to luminaire. Phillip Hannesen, Digital Transformation Manager Production, adds: "With the WLS15 line luminaires we have found an elegant and cost-effective solution. They are located behind the shelf plate, while the cabling is organised via the rear. This allows the assistance system to be perfectly integrated into the standard C-parts shelf and is practically invisible."
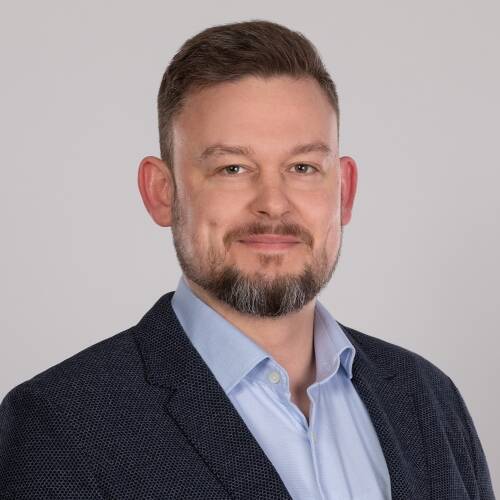