The clutch: air gap adjustment made easy
Patented function of KEB Automation facilitates commissioning
A simple start-up instead of making lengthy adjustments: This is made possible by an innovative clutch from KEB Automation. Thanks to a patented process, the coupling is able to automatically adjust the working air gap. Otherwise extensive adjustment steps by the user are no longer necessary. How exactly does the process work and how do users benefit from it in practice?
Within a clutch, the so-called working air gap is initially inconspicuous. But during operation it plays an important role. The air gap separates the armature disk from the rotor and must be set so small that the forces of the magnetic field are as high as possible. “At the same time, the working air gap must also be large enough so that the armature disk and rotor do not come into contact with each other during operation. This can lead to wear and damage in the clutch,” says Thorsten Nolte, Sales Engineer Brakes and Clutches at KEB.
A concrete consequence would be an unintentional increase in the air gap and, as a result, a reduction in the force of the magnetic field. Not least for these reasons, an air gap of between 0.2 mm and 0.5 mm is generally used. Until now, the user typically had to adjust the gap manually or semi-automatically.
Working air gap is set automatically
KEB's innovative process, however, takes over exactly this step – and does so completely automatically. This eliminates the need for time-consuming component measurements and specific working air gap settings. The “plug and play” principle enables quick and easy commissioning of the coupling. Customers can thus optimise their processes and reduce sources of error.
“The automatic adjustment of the working air gap prevents new contamination from entering the customer's system. The pre-set air gap is maintained until commissioning," says Nolte. "Each clutch unit has successfully completed a complete run-in cycle and is immediately ready for use in the application.”
Friction linings do the work
The mechanism developed by KEB thus offers a number of advantages for the user. The underlying mode of operation is based on the two friction linings located in the rotor of the clutch. The outer lining is used for torque transmission. The inner lining, also called the sacrificial friction lining, is used to adjust the working air gap during final assembly of the unit.
The armature hub meets the rotor with the friction linings. Through a defined programme sequence, the sacrificial friction lining is now reduced until the ideal working air gap is achieved. With no further action required on the part of the user, the coupling is now ready for direct use in the desired application.
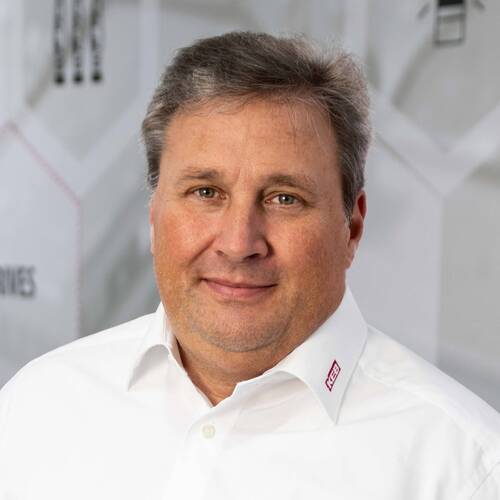