Lower rejects through optimised press
KEB Automation supports high-end servo press
Customers can save up to 70 percent of energy costs with a newly developed servo press that Michael Stangier and his company MS-Hydraulik have developed for vehicle construction and implemented together with an Italian partner. The company turned to KEB Automation as a partner for servo drives and energy efficiency for this special machine technology.
When planning the high-end servo press, Stangier relied in particular on KEB's Active Infeed Converter solution (AIC, also called Active Front End). This enables both energy intake from the grid and energy output to the grid. Overall, the KEB portfolio offers scalable solutions for charging and storage technologies from 11 kVA to 1,000 kVA. Ten COMBIVERT F6 Servo Drives as well as two COMBIVERT S6 Servo Drives and two F5 Active Infeed Converters are used in the press. The bottom line in this case is a press capacity of up to 1,200 tonnes, which enables large individual parts to be made of steel for vehicle construction.
A key advantage is that not only energy costs can be saved, but also the number of rejects can be reduced thanks to a very precise production method. In the future, the company wants to establish the technology further, reports MS-Hydraulik CEO Michael Stangier. “We want to show what possibilities there are to build more efficient presses. KEB is a loyal and reliable partner in the planning of the implementation, whose ability to work in a team I appreciate very much,” he says. Davide Fusari, responsible sales engineer at KEB: “This machine is an absolute premium product due to its size and performance – also worldwide. Our high-end drive technology and the supply and regeneration system, the F5 Active InFeed Converter, are installed there.”
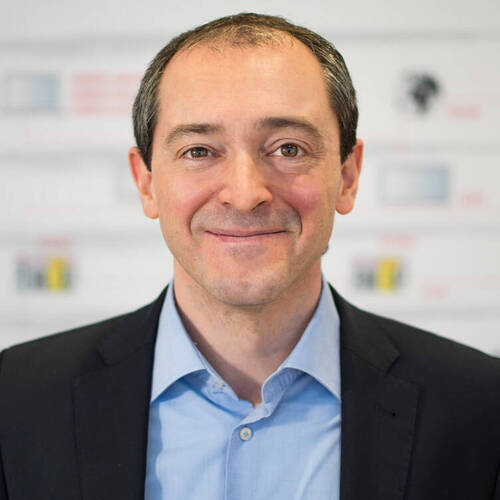