First cobot is used in KEB production
Which role brakes from KEB play in robotics
KEB Automation has put a cobot – a collaborative robot that works in direct contact with humans – into operation for the first time at its headquarters in Barntrup. The industrial robot is being used in electronics production as part of a pilot project and is already providing exciting insights. This was accompanied by a number of obstacles that had to be taken during commissioning. And although this is the first cobot at KEB, there is another reason why the topic is anything but unfamiliar to KEB.
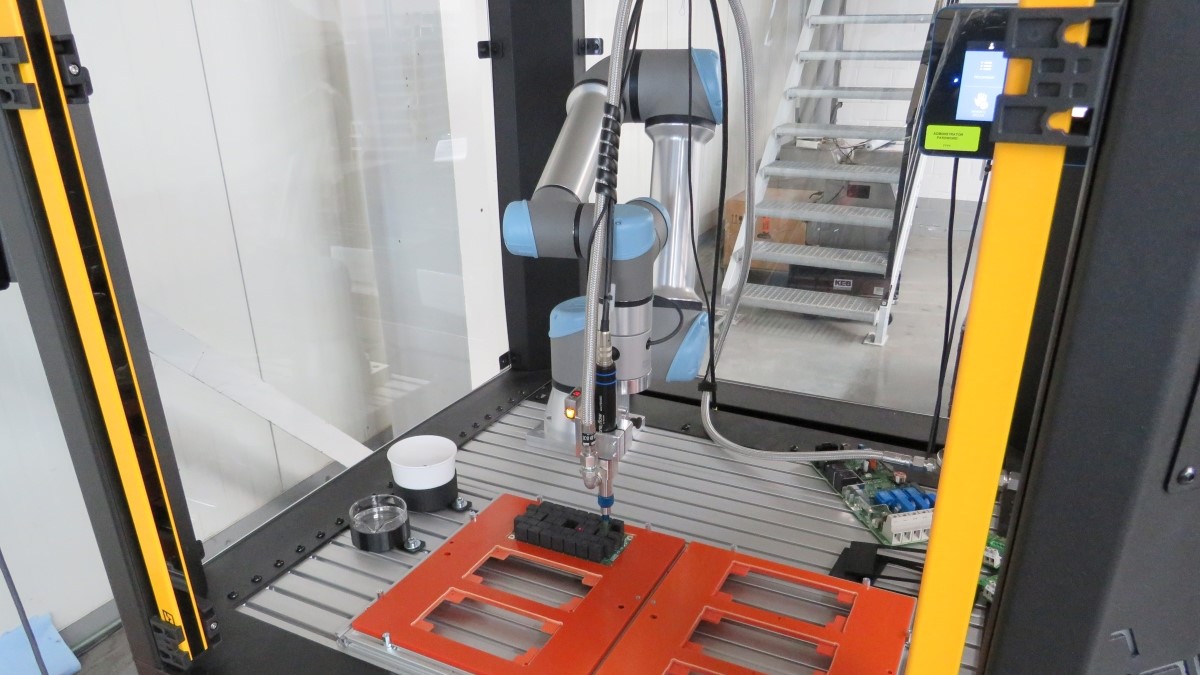
The cobot is being used in cooperation with the tech start-up Unchained Robotics from Paderborn. The robot, called “MalocherBot” (meaning: “working hard bot”), is used at KEB in the final stage of circuit board production to fix the assembled components with silicone and thus make the circuit boards more resistant to vibrations. The aim of the pilot project is to gain experience in working with cobots and evaluate the strengths and weaknesses of the technology. The use of robots is being supervised by KEB's Industrial Engineering department.
Timo Müller specialises in production processes within this department and says: “First of all, we want to test cobots in practice so that we can use them better and in a more targeted manner in future projects. Ultimately, of course, the aim is to increase employee productivity with the help of the cobot so that it can process more circuit boards in the same amount of time without putting additional strain on the employee.” However, it is already apparent that the cobot can provide efficient support for some circuit boards, ensuring that employees can carry out other tasks in the meantime.
Requirements and challenges
KEB placed special requirements on the cobot in the run-up to commissioning. It had to work as quickly as possible and ensure work safety. More precise dosing was required to reduce the amount of silicone needed. The high precision should also ensure that the quality of the circuit board is consistently good. Last but not least, the cobot should be as easy to operate as possible and it should also be possible for non-experts to create a new programme after a short training period. KEB and Unchained Robotics already worked together during the development process and close coordination was also essential during commissioning, which was quite challenging. On the one hand, this was due to the CE approval and the mechanical structure of the cell. But it was also due to the fact that KEB's Industrial Engineering department usually builds systems that work with very high currents. This resulted in unusually high standards, which the cobot also had to fulfil.
But the effort was worth it. The industrial robot recently completed its first series order. “It is very easy to operate and the cobot will be able to process many circuit boards in the future. Thanks to the high precision, the amount of silicone required can be reduced by up to 50 per cent in some cases. We have also been able to identify where there is still potential for optimisation. We are optimistic that more cobots will find their way into KEB's production in the future,” says Müller. It is conceivable, for example, that the cobot could take over the coating of hard-to-reach areas on circuit boards, which is currently still done manually. Activities in final assembly and THT assembly or taking over pick and place tasks are also areas in which cobots could be used in the future.
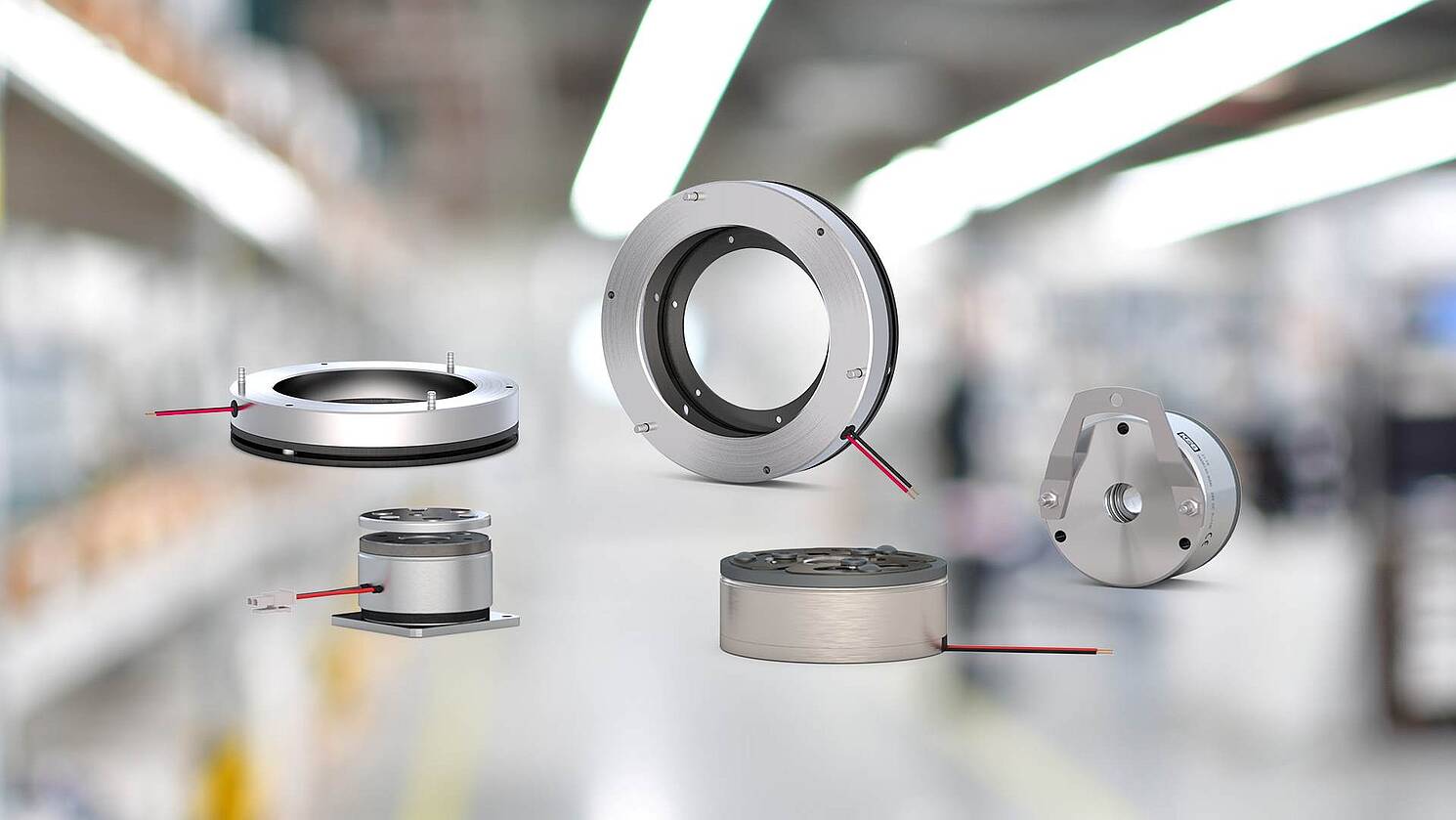
Brakes for robotics applications
KEB knows first-hand the requirements for cobots in terms of compactness, repeatability and positioning accuracy. This is because KEB brakes have been at home in the world of robotics for a long time. Standard and customised solutions for industrial robots, actuators and cobots are realised with the highest quality and flexibility for the user. State-of-the-art development processes and decades of brake expertise ensure products that work reliably over the entire lifetime of the respective robotics application.
“Safety is one of the most important requirements in automated production. If you think about a possible power failure, for example, it is important to maintain the position of the robot arms and prevent the robot axes from collapsing. For precisely these and other cases, we develop fail-safe brakes such as the COMBISTOP or COMBIPERM, which are customised to customer requirements,” says Kevin Zysk, Head of Sales Brakes and Clutches at KEB Automation. A special feature of collaborative robots is that the installation space is usually very limited. Whereas in industrial robots the safety brake is installed on the servomotor, in cobots the brake is often located inside the articulated arms. Here too, KEB supports users by customising the installation conditions.
What requirements does robotics place on brakes?
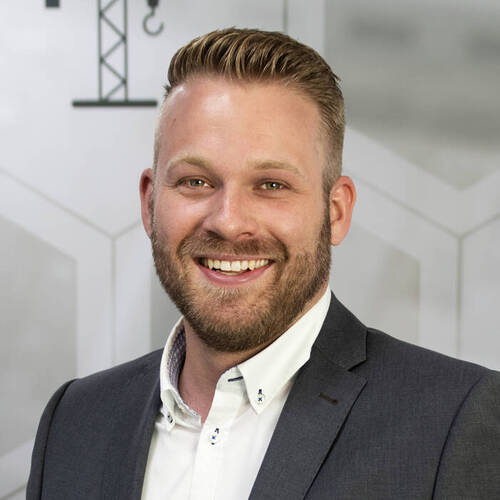