Cutting, dosing and packing with safety drives
3 Questions on food and packaging machinery
Fabian Fischer, Team Leader Application Sales at KEB Automation, explains in an interview what challenges food and packaging machinery holds in store for drive and automation solutions and how these can be mastered. In particular, functional safety concepts are of great importance.
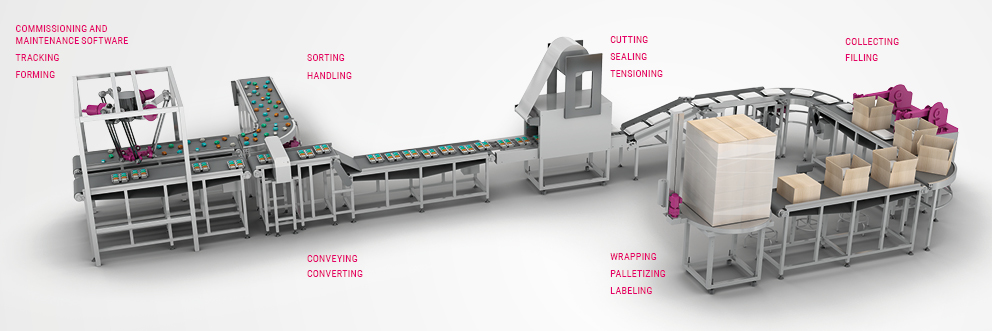
What requirements do drive components used in food and packaging machines have to meet?
Fischer: Pack & Food applications are characterised by harsh environmental conditions. In many cases, the machines are cleaned with aggressive washing substances and high pressure. Motors, frequency inverters and controllers must therefore be robust and hard-wearing. The circuit boards in the current series of frequency inverters from KEB Automation are therefore equipped with a protective lacquer specially developed for these environments. And our HMI control panels, for example, are made of stainless steel and have a high degree of protection of IP69K. High-pressure cleaning and even temperatures of 50 degrees Celsius therefore do not affect the devices. Performance is also important: Food and packaging machines must ensure precise cutting, dosing, mixing and filling with the shortest cycle times. For this purpose, we offer compact and energy-saving dynamic drives with high overloads and precise control.
Especially in the Pack & Food sector, functional safety plays a major role. How can hazards be reduced by drive systems?
Up to now, safety technology was often set up decentrally with external safety modules. These were expensive, complex to wire and required space in the control cabinet. At KEB, we build functional safety concepts in a smart way. Functions such as “Safe Torque Off” (STO) or “Safely-Limited Speed” (SLS) are integrated in our COMBIVERT drive controllers and can be selected on a modular basis. Wiring is not required if a safety controller with, for example, Safety over EtherCAT or PROFIsafe is used. With many speed-based safety functions, the safe encoder can even be eliminated. With our integrated safety function "Safe Door-Lock Control" (SDLC), door switches of food processing machines with knife drives, for example, are only released when the knife has come to a standstill. An external module for monitoring is not necessary.
KEB Automation offers complete system solutions for food and packaging machinery. What advantages does this offer users?
From HMIs and controls to drives, motors and brakes, we implement drive solutions from a single source. The individual components are optimally matched to each other, resulting in maximum machine efficiency. And since, for example, the motor and inverter harmonise perfectly, we also comply with the stricter eco-design guidelines. This is matched by the fact that our drive controllers are equipped with the new IE2 energy efficiency label according to the EN 61800-9-2 standard. Another advantage for the machine builder is that there is only one contact person for all matters concerning the drive. The flexibility of interfaces to components from third-party suppliers is retained in all this, in order to integrate components effortlessly into existing systems.
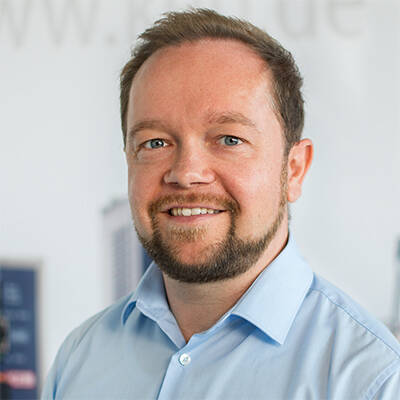