An industrial heat pump – mechanical vapour recompression
Piller Blowers & Compressors
For over 30 years Piller Blowers & Compressors is a specialist for mechanical vapour recompression. The company’s flagship product – PILLER high-performance blowers – can be found in various applications within the process industry around the world. These systems are driven by a solution from KEB, but how does it all work?
“The resulting process steam, also known as vapour, is heated to a higher temperature with a radial blower, which in turn results in a higher level of energy. This is then fed back into the process as fresh heating steam, which essentially makes it an industrial heat pump,” explains Dr Steffen Kuberczyk, Global Sales Director at PILLER. “This ensures that the energy within the steam is not lost, as only the electrical energy required to increase the temperature remains to be applied. Our latest product for this high-growth market of mechanical vapour recompression is the VapoFan – an innovative, high-performance blower for mass flows ranging from 200 to 5000 kilograms per hour and an efficiency level of 85 percent,” adds Kuberczyk.
Large amounts of process steam are commonly needed in the process industry. The Blowers are used in evaporation processes, distillation, crystallisation and drying – in breweries, sugar-, salt-, pulp- or chemical industry as well in dairy industry for the production of milk powder.
Reducing steam consumption
The high efficiency of these blowers, which are working as compressors, is realized by the perfectly optimized drive system. In case of the newly developed PILLER VapoFan, the drive system consists of a synchronous motor – specially developed by PILLER – in combination with COMBIVERT Drive Controller from KEB Automation, including a sine-wave filter. Fabian Fischer, Head of KEB Application Sales process industry, summarizes the advantages:
“Through simulation, we have jointly determined the optimum combination of drive controller, sine-wave filter and synchronous motor and thus reduced electrical losses to a minimum.” The mechanical vapour compression lowers the high steam consumption – the process is a reliable and effective energy saving method.
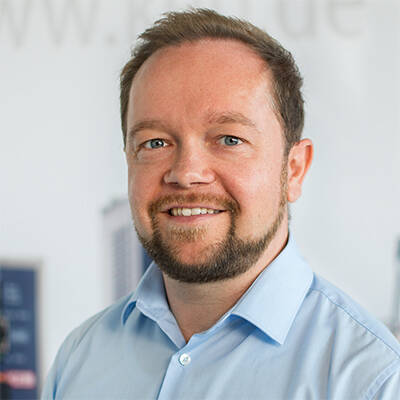